What Makes Wicon’s Welding Positioners a Game Changer in Fabrication?
Welding positioners have long been recognized for their vital role in modern fabrication, and Wicon has distinguished itself by offering systems that combine precision engineering with advanced digital controls. When you examine the benefits of a welding positioner in an industrial setting, it becomes clear that devices like the Conventional Positioner and Head-Tail Stock are central to enhancing overall weld quality. These positioners allow the operator to secure and manipulate heavy workpieces with ease, ensuring accurate alignment and consistent rotation even when the geometry is complex. Wicon’s approach to these systems is not merely about holding a component in place; rather, it is about optimizing the welding process by automating movements that reduce operator fatigue and human error. By integrating digital speed indicators and remote control panels into these machines, Wicon’s products enable real-time adjustments that contribute significantly to the consistency and quality of the final weld.
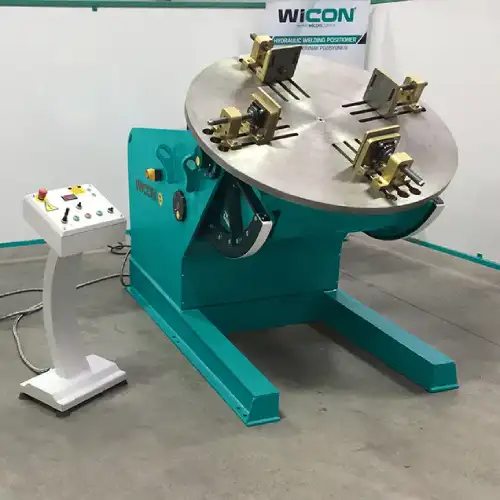
How Do Specific Wicon Models Address Diverse Welding Needs?
A closer look at the lineup of Wicon welding positioners reveals a strategic approach to catering to a wide range of fabrication challenges. The Conventional Positioner has been a reliable workhorse in many workshops, providing steady and reproducible motion during welding. Similarly, the Head-Tail Stock model offers specialized features tailored for welding applications that require symmetry and balance in workpiece orientation. Yet the range does not end there; Wicon’s Hydraulic Positioner introduces the advantages of fluid power for smoother, more controlled movements under heavy loads, proving beneficial in applications where precise pressure modulation is essential. The H Type Positioner, L Type Positioner, and U Type Positioner expand the portfolio further, offering different structural configurations to best suit the shape and welding requirements of various materials. Each model is designed with the same underlying philosophy: to minimize manual intervention while maximizing consistency and safety. Operators who have used these machines report that the increased maneuverability, due in part to features such as adjustable rotating speed and digital feedback, has a direct positive impact on the quality of complex weld joints.
Why Are Technological Advancements Central to Wicon’s Positioner Systems?
Technological integration is at the heart of what makes Wicon’s positioners stand out in competitive industrial environments. The incorporation of digital speed controls not only enhances the precision of the Conventional Positioner and Head-Tail Stock models but also allows for seamless adjustments during the welding process. For instance, when welding on curved surfaces or when working on a fabrication line with continuously varying conditions, having an interface that provides instantaneous feedback is critical. The Hydraulic Positioner takes this concept even further by using hydraulic power to fine-tune movements, offering a level of control that is particularly useful when working with heavy and unwieldy materials. The H Type, L Type, and U Type Positioners each feature unique structural designs, yet they all rely on similar digital controls and remote management capabilities. This consistency in control interfaces across different models simplifies the training process for operators while enhancing productivity. Moreover, the digital interfaces enable advanced functions such as programmable speed cycles and remote troubleshooting, which contribute to a reduced likelihood of errors and minimize downtime—a crucial factor in high-volume production settings.
What Are the Advantages and Drawbacks of Integrating These Positioners into the Welding Process?
The advantages of using Wicon’s welding positioners extend well beyond improved precision. By automating the movement of workpieces through systems such as the Conventional Positioner and Head-Tail Stock, production becomes not only faster but also safer. Operators do not have to repeatedly lift or reposition heavy components by hand, reducing the risk of injury and boosting overall workplace safety. The Hydraulic Positioner adds another layer of benefit by offering smoother operation for heavy-duty applications that would otherwise require a significant amount of manual control. The differentiated designs found in the H Type, L Type, and U Type Positioners ensure that fabricators can select a system that is best suited to their specific production needs and material types. However, it is also important to consider some challenges. The initial cost of acquiring one of Wicon’s high-end positioners may be relatively high compared to simpler mechanical solutions. The sophisticated technology integrated into these machines requires thorough training for operators, who must learn to navigate digital panels and programmable logic controls, as well as a commitment to regular maintenance. The complexity inherent in digital systems, while improving precision, sometimes means that troubleshooting malfunctions can lead to extended downtime unless technical support is promptly available. Thus, while the benefits in terms of product quality, operator safety, and production efficiency are considerable, they must be balanced against the investment and ongoing maintenance demands.
How Do These Positioners Affect the Overall Workflow in a Welding Environment?
The integration of Wicon welding positioners into production processes leads to clear and measurable improvements in workflow efficiency. Conventional and Vertical Positioners enable stable and precise positioning of workpieces, resulting in consistent enhancements in welding quality. The uniformity of weld seams and the homogeneity of weld penetration are concrete indicators of this improvement. Such consistency is particularly critical in high-volume production environments, where positioning errors can lead to significant welding defects.
Remote control systems supported by digital interfaces allow operators to monitor the process and make necessary adjustments from a safe distance. This minimizes exposure to high temperatures and physical strain, thereby improving workplace safety. At the same time, operator fatigue is reduced, leading to more sustainable and efficient production throughout the workflow.
In the long term, continuous improvements in welding quality and enhanced operator comfort significantly reduce overall production costs. Although the initial investment and maintenance requirements may seem demanding, the resulting gains in quality, safety, and efficiency make these systems highly profitable over time.
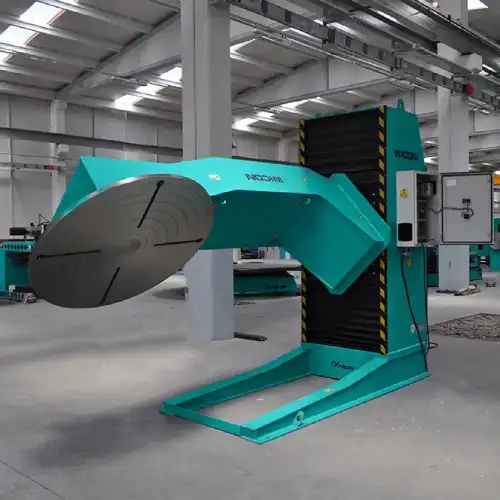
Why Is Wicon a Trusted Name in Welding Automation?
Wicon’s reputation in the welding industry is built on its innovative approach, rigorous quality control, and continuous efforts in product development. With models such as Conventional, Vertical, Hydraulic, H-Type, L-Type, and U-Type Positioners, Wicon successfully integrates advanced digital technologies with robust mechanical designs—forming the foundation of its customer-oriented success.
Users recognize that Wicon positioners are engineered to withstand the demanding conditions of modern production environments. These systems not only minimize welding defects and reduce material waste and rework, but also significantly lower labor costs and the need for manual intervention. As a result, both the quality and efficiency of production processes are substantially enhanced.
The integration of advanced digital interfaces and modular designs compatible with a wide range of applications brings the power of automation to the shop floor, while simultaneously improving safety and reducing operator fatigue. In today’s competitive market, producing high-quality welds while protecting operator health and safety has become a critical priority. Wicon’s innovative solutions provide a reliable foundation for welding operations, enabling manufacturers to meet high standards consistently.
Ultimately, whether using Conventional, Vertical, H-, L-, or U-Type Positioners, manufacturers experience significant improvements in weld quality, operator safety, and overall productivity. Although initial investment and maintenance requirements may pose early challenges, the long-term benefits—improved precision, reduced labor demand, lower operational costs, and streamlined workflows—more than justify the investment. Modern manufacturing facilities are increasingly adopting Wicon’s comprehensive range of positioners as a forward-thinking, strategic solution for optimizing their welding operations and staying ahead in a competitive landscape.